Genesis of the Mini-Max tracker project
Integrated dual-axis solar tracker system with common drive and ‘Mini-Max’ control
Analysis and objectives
Work on the project was initiated in 2020. Knowing the well-known problems faced by dual-axis solar trackers, after analysing their causes, we set ourselves the most important objectives:
minimization of failure susceptibility
minimization of service issues
minimization of production costs
maximization of energy yield
Preliminary analysis has already shown that the cause of operational issues lies in the drives and their placement. While visually striking, their principle of operation—resisting wind gusts with a static force applied to the PV panel frame—makes them prone to failures. Repairing these failures often requires heavy equipment or the disassembly of almost the entire tracker. This interaction between the frame and the drives can be compared to driving a car over potholes with a rigid, non-cushioned suspension.
After a year of work on the test installation, a completely new, innovative drive system was developed under the name "A.S.N.T." Active Tracker Drive System. In addition to relocating the drives outside the trackers—turning them from direct to indirect drives, thereby completely eliminating the negative impact of the frame on their operation—we implemented the patented A.S.N.T. gear system, which absorbs strong wind gusts impacting the frame. This eliminated a wide range of overloads and vibrations that contribute to failures, ensuring smooth and trouble-free tracker operation. Additionally, we developed a unique, unprecedented feature that allows multiple dual-axis solar trackers to be connected in series, in any number, using a single shared drive for each axis and a single control system. In June 2021, we filed a patent application with the PUP for protection. After a positive preliminary assessment, in June 2022, we submitted an international protection application to WIPO. In June 2023, we were granted a 20-year PUP patent.
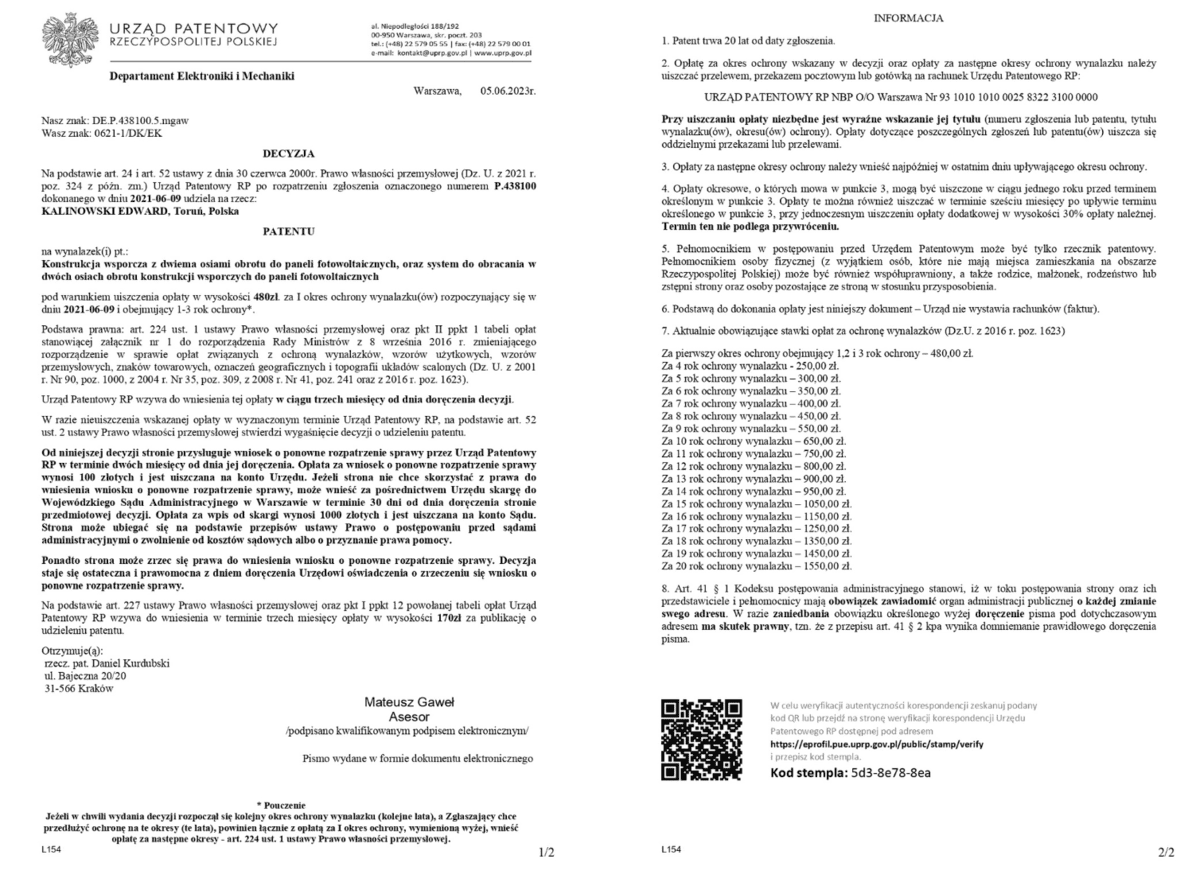
Decision
Based on Articles 24 and 52 of the Act of June 30, 2000, Industrial Property Law (Journal of Laws of 2021, item 324, as amended), the Patent Office of the Republic of Poland, after reviewing the application numbered P.438100, filed on 2021-06-09, grants to: KALINOWSKI EDWARD, Toruń, Poland
A PATENT
for the invention(s) titled:
A support structure with two axes of rotation for photovoltaic panels, and a system for
rotating support structures
Internal Research and Development work.
Mechanics
Economics
Operation and Service
Effectiveness tested by empirical method
To ensure reliable results in testing the performance of the dual-axis Mini-Max tracker system, we divided it into two independent installations, each with a capacity of 4.8 kWp per tracker. One was equipped with bifacial panels, while the other used monofacial panels. Additionally, a fixed installation with the same 4.8 kWp capacity was set up nearby. Each installation operated with an individual inverter.
After a full year of operation, the tracker with bifacial panels achieved a 58% higher energy yield compared to the fixed "south-facing" installation and an 11% higher yield than the tracker with monofacial panels. What stands out is the significantly greater energy production in the morning and late afternoon hours, reaching up to 1,400%—for example, on June 12, 2022, at 19:00, the fixed installation generated 0.21 kWh, while the Mini-Max bifacial installation produced 3.27 kWh.
These results led to the development of the "30% Rule," which encapsulates the benefits of using dual-axis trackers.
Reducing the power of a PV installation on Mini-Max trackers by 30% compared to a static installation means that, while maintaining the same target efficiency, we move 30% of the output from peak to off-peak hours, thus reducing the need for energy storage and photovoltaic panels by 30%. This means that, in this configuration, a static installation is about 30% more expensive than a tracker installation.
Ecology and carbon footprint
It is well known that energy generation from PV panels is the most environmentally friendly solution. However, this is true only when the generated energy is consumed immediately. While energy storage is necessary and justified, it also carries an ecological footprint, particularly in the case of commonly used lithium-ion batteries. Additionally, the economic factor becomes increasingly significant.
The principle above reflects this reality. Assuming an optimistic 15-year battery lifespan, over a 30-year period, the batteries would need to be replaced twice, undergoing a full "cradle-to-grave" cycle, along with energy transmission losses and costly disposal. In contrast, trackers, which operate on a short "cradle-to-gate" cycle, generate part of their energy outside peak hours, allowing for immediate consumption. After 30 years, only the panels would require disposal, while the trackers, classified as scrap metal, would not be waste but rather a valuable raw material.
Since energy storage cannot be entirely avoided, it should be minimized. In the case of dual-axis Mini-Max trackers, this approach is further justified from an economic standpoint.