common drive and control
Dual axis Solar Tracker System
Biaxial tracking systems are familiar to anyone interested in photovoltaics. More commonly known solutions, however, besides the huge advantage of more than 50% higher yield from the same number of panels, struggle with a number of disadvantages.
What problems do you have to deal with?
- Price - which, due to the design and technology, is unfortunately high. It is known that the larger the rack, the higher the yield, and this in turn necessitates the use of heavy equipment both for installation and for troubleshooting
- Discouraging cost of failure removal - A two-axis tracker will be prone to failures due to the difficult working conditions at times. Therefore, it is important, first, to prevent failures, and second, to minimize the cost of repairing them.
We know the solution
The goals we set for ourselves, in order of importance to the project:
1. Easy service access.
2. Simplifying drives along with reducing susceptibility to failure.
3. Achieve the lowest possible manufacturing cost.
4. Maximize the capabilities of the tracker.
Latest news from Tracker Mini-Max
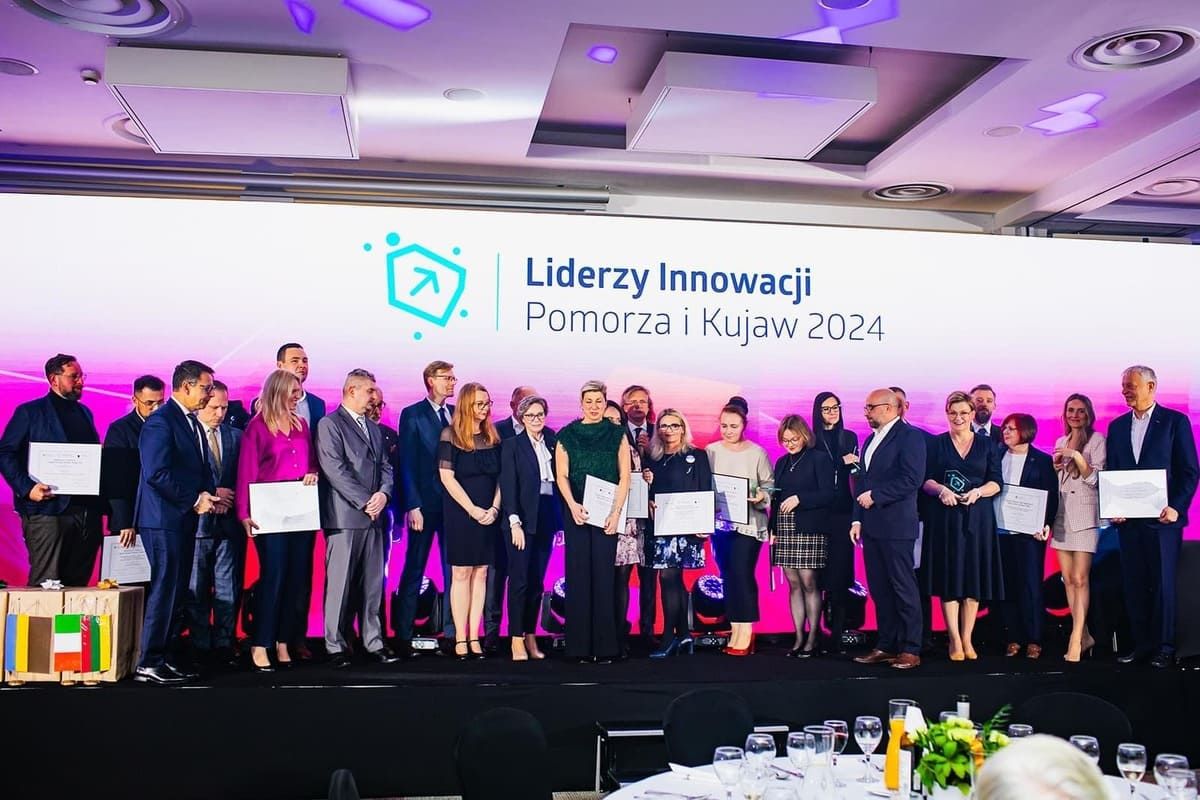
Tracker Mini-Max Sp. z o.o. wyróżnione w konkursie Liderzy Innowacji Pomorza i Kujaw 2024
Problem analysis
It is known that as the power of the tracker increases, the surface area of the photovoltaic panel rack increases, and thus the base needs to be strengthened more.
The first thing that gave rise to thought was the disproportionately higher increase in the weight of the whole device in relation to its power. For example, a tracker of about 10 kWp weighs 1 ton, 20 kWp weighs 2.5 tons, and 32 kWp is already 4.5 tons.
Next, you need to think about the drives used. Most solutions use expensive planetary bearings, but worst of all, replacing them is like putting up a tracker from scratch.
The second drive is usually a linear actuator, which, in order to fulfill its role, must be robust and therefore expensive.
Conclusions
These comments influenced the overall design thinking. We realized that a lot needed to be changed to make the unit work at its best.
First, was the optimal size of the rack with panels, perhaps the least concerning change, but having a big impact on the design.
The next is to modify the drives while keeping their design and operation as simple as possible.
The next is to modify the drives while keeping their design and operation as simple as possible.
Further on is integrity and compatibility. Optimized by the size of the rack, the so-called MiniTracker, should be configured in an integrated system of a certain number of MiniTrackers, fine-tuning the best joint drive and control system optimally.
This is seemingly simple, but required a lot of testing.
Realisation
The first test set of MiniTrackers built gave the answer that the designed drive system in the North-South directions was the right one.
An East-West drive remained to be developed. One very simple, but as simple as it was effective, decision to modify the "worm gear" resulted in solving the most important first point of the project easy service access".
Effect
Integrated system of two-axis solar trackers with common drive and control "MINI-MAX"
Why it's better?
Easy, uncomplicated service access
Almost every possible emergency can be fixed by one person in no more than 0.5 to 2 hours.
Simple installation
The height of the minitracker is just over two meters. Installation without heavy equipment for 2-3 people in one day including panels. The foundation is not involved.
Manufacturing cost
The weight of one unit is about 0.5 tons, for which 5 tons of steel are needed for ten integrated trackers with a total output of 60 kW. This requires only two drive units and one control.
Trouble-free operation
The installed test device has worked in conversion for ten years / at 100 daily cycles per day /. After eliminating a few shortcomings, the last more than five years without problems. We anticipate once a year inspection, and daily indicated monitoring with preventive notification in case of a problem.
Maximum yield
The above steps and improvements result in maximum utilization of the device on an annual basis, and the use of Bifacial panels in addition, in our tests, yields about 15% more.
Patent protected solution
The mini-max tracker, which allows maximum energy recovery from the sun at minimal cost, is our proprietary, patent-protected solution
Tracker Highlights
"Increasing tracker efficiency by increasing the number of panels" is the conclusion we reached after analyzing the available solutions.
However, we pointed out that the cost of operation, installation and failure rate of such a project increases with increasing power.
First, we built a so-called "mother" tracker , which supports the other so-called "daughter" trackers. After adjusting its maximum optimal size, we refined the seemingly extremely simple drives.
Results
Comparing the tracker with a ground/ground installation, we find a number of advantages:
- we produce 50% more energy,
- installation half as much (we use less pv panels when installing),
The monotonous production of the tracker, gives you the opportunity to consume energy on a regular basis, in the case of ground we have the highest production at 12 noon, (the installation must be 50% larger, that is, overproduction in the midday hours).
Such a design is also safer because the tracker in high winds sets itself in a safe position (horizontal).
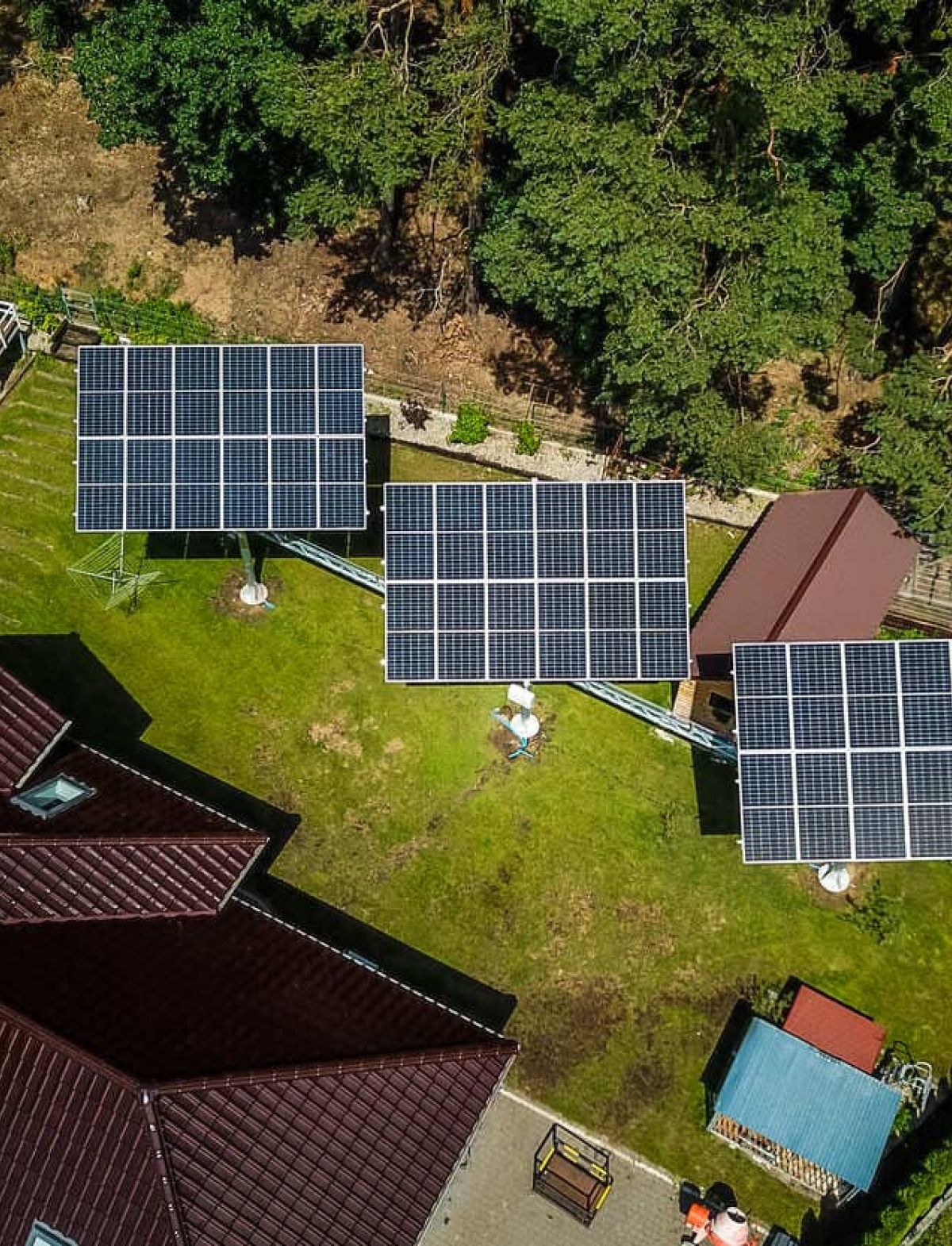
Smart
Space
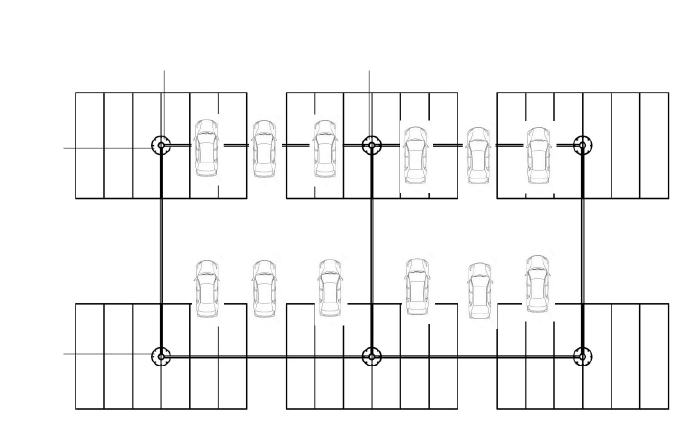
Wherever you need
We've come a long way in finding the optimal solution for energy harvesting while thinking about minimizing costs, and now we have a better way to use it. You can save a lot of space and still get 60% more energy than with a stacionary panel.
Highlights
The use of photovoltaic trackers on an elevated structure, along with trusses, will allow the use of the space underneath.
The given solution will allow one hundred percent use of the space, as well as the use of the energy produced, directly for consumption, which will relieve the burden on the energy infrastructure, thanks to the use of dual-axis trackers, or at least 1-axis trackers, we have the possibility to produce energy for a longer period of time during the day, and thus the installation can be smaller and less invasive to the infrastructure.
of space used
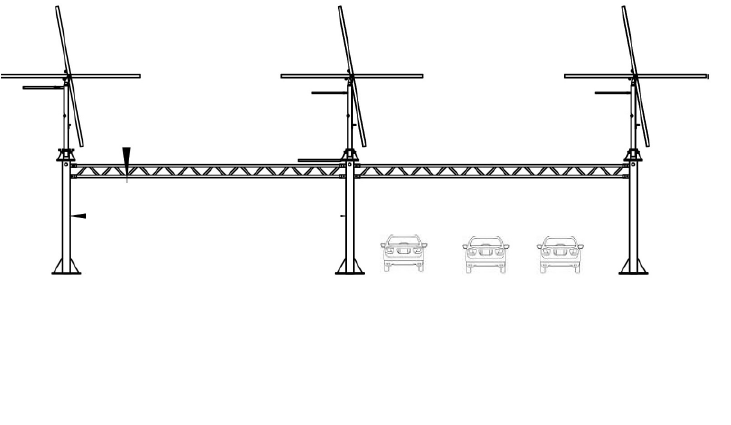
The solution will find application in places such as:
- Parkings of Supermarkets, which will generate energy for the stores, or allow you to charge your electric car,
- Parkings of gas stations, various companies or institutions,
- Houses,
- Hotels,
- Railway tracks, using the space above it for an installation that will produce energy to power a train/tram
-
Standard grunt panel
-
Mono
-
Tracker Mini Max
Integrated system with one drive and one control
The first test set at the moment works during the day, and at night "works" the daily working cycles. Currently, it has worked about 5 years of daily operation / about 2,000 cycles /. The target, we anticipate, set should consist of 8 to 10 units and power from 50 to 63 kW.